Driver or damper? The battery has become a crucial factor in the development of electric vehicles. Supposedly small innovations can give the entire drive system a substantial boost. Two examples from Mersen
Ten years ago probably no one would have been able to predict the huge present-day popularity of electric vehicles. Experts assume that 30 percent of motor vehicles sold in the year 2030 will be electrified. This will also mean a sharp rise in the demand for batteries.
Batteries are the crucial factor in electric vehicles. They are the most expensive part of an electric vehicle and can become a driver or damper in the development of electric vehicles, depending on how successfully the rising demand can be met. “That creates huge pressure to improve the cost structure of the battery architecture, to make it possible to achieve the necessary growth,” explains Pierric Gueguen, Global Business Development Director at Mersen, which specializes in electric safety systems.
Despite all the innovation pressure on the battery, Gueguen points out that safety must always be the top priority. Short circuits in electric cars can start a fire in the battery, which then spreads to the entire vehicle. “Burned-out cars on the roadside are not an uncommon sight,” says the expert. That is why safety must always be the top priority in efforts to optimize battery architectures.
Mersen has been specializing in safety systems for electric vehicles for many years. The company offers tools for both safety and monitoring of all components and processes involving electricity in electric vehicles: from the battery to the inverters and the overall vehicle, as well as the DC quick-charge station. Mersen offers battery fuses for all levels of the battery – the single cell, the module and the entire battery pack – as well as for secondary consumers such as heating and air conditioning. Now the company is introducing two technological developments that definitely have the potential to provide impetus for electric vehicles overall: InBat fuse and InfiniCell.

The InBat Fuse combines the advantages of two technologies: thermal performance, ease integration of a bus bar and protection capability of a fuse
Photo: Mersen
Module Level fuse and bus bar
The InBat fuse is a hybrid consisting of a fuse and a bus bar. Mersen has extensive expertise in two fields of technology: electric fuses and bus bars. Both competences were integrated in the development and allow to keep the best of each technology, thermal performance, ease integration of a bus bar and protection capability of a fuse. “InBat Fuse is integrated into the heart of the battery modules, so to speak, as a protective device. This is quite unique and makes work easier for our customers,” Guillaume Lemmel, Mersen’s EV SBM Project and Design Group Leader, emphasizes.
Batteries in electric vehicles are generally protected against short circuits by different devices: contactors, fuses or pyro switches that are integrated in the battery disconnection unit (BDU). In the event of a fault, these tools insulate the battery from the rest of the vehicle.
The InBat fuse performs additional safety functions to the BDU. For example, it is simply closer to the single battery cell and can respond more quickly if there is a problem with the cell. The InBat fuse also protects the life cycle of the battery up until the battery is installed in the vehicle and is connected to the BDU – i.e. from the connection of the single cells to the module and of the modules to the battery pack, as well as any test procedures (for example UN 38.3) and transport of the battery to the automobile manufacturer.
InBat fuses are designed for voltages up to 250 V DC and short-circuit currents up to 13 kA, and are compatible with all types of battery cells – cylindrical, prismatic and pouch cells. “The InBat fuse is the latest innovation from our R&D department, which developed the fuse in close cooperation with customers in the automotive sector,” Pierric Gueguen relates.

The InBat Fuse combines the advantages of two technologies: thermal performance, ease integration of a bus bar and protection capability of a fuse
Photo: Mersen
Four times faster assembly
As new as the InBat fuse is, so time-proven is the other Mersen innovation, which the company however is now introducing to the market in a much more optimized second generation: the InfiniCell. Mersen developed the standardized battery cell connection platform in cooperation with the German manufacturer of laser welding systems F&K Delvotec. This very thin laminated bus bar consists of a copper or aluminum layer that is surrounded by in insulating layer. It is suitable for connecting all types of battery cells and performs both connection and monitoring functions. It reduces safety problems, for example short circuits during module assembly and welding, and features good shock and vibration resistance as well as resistance to temperatures of +105 °C and higher.
“Furthermore, two factors make the InfiniCell a pioneering technology that could be decisive in shaping the future of battery architectures,” explains Gueguen.
- First: The connection platform is suitable for all standard assembly processes (wire bonding, ribbon bonding, ultrasonic welding and laser welding) and it allows an assembly process that is up to four times faster than conventional welded connections with cables or ribbons.
- Second – and this is what makes the new InfiniCell generation special: Due to a patented process, the bus bar allows connection of plus and minus poles of the battery cells on the same side. This further simplifies the connection of the cells in the production shape and also offers advantages in the architecture. The bottom of the module remains completely free, so that the temperature management system can be installed there. That not only simplifies and accelerates the assembly process, but also reduces the space needed for the module.
Electric vehicles require ever more storage applications with increasing requirements for power density. Technologies are therefore needed that reduce space requirements without restricting efficiency. “InfiniCell is an ideal tool for this,” Gueguen emphasizes.
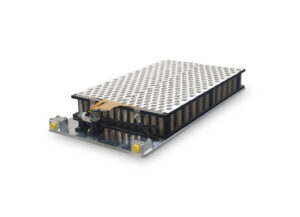
The new generation of InfiniCell allows the connection of plus and minus poles on the same side, thus speeding up assembly and optimizing the architecture of the battery module
Safety at different levels
“The issue of battery safety can be approached at several different levels,” Pierric Gueguen says in summary. “At the level of the single battery cell, the battery module or the battery pack.” That is a matter of the safety strategy and requires different safety tool modules. The modular concept is also retained with InBat Fuse and InfiniCell, which of course can also be used in combination. “Mersen has long assumed the role of developing exactly the safety tools that are needed for the different safety architectures and strategies of its customers,” emphasizes the expert. Manufacturers and suppliers therefore work together to set new developments in battery technology in motion, thus giving a powerful boost to continuing progress in the electric vehicle sector overall.